Tiết kiệm tiền tỷ nhờ áp dụng thành công hệ thống LEAN
Nhằm giảm chi phí sản xuất, đồng thời, nâng cao năng suất và chất lượng sản phẩm, Công ty TNHH Nệm Ưu Việt đã lựa chọn áp dụng hệ thống LEAN, với sự hỗ trợ của Trung tâm Kỹ thuật Tiêu chuẩn Đo lường Chất lượng 3 (QUATEST 3).
.jpg)
Khu vực sản xuất trước khi cải tiến Ảnh: QUATEST 3
Nguyên nhân gây lãng phí
Được thành lập từ năm 1993, Công ty TNHH Nệm Ưu Việt có kinh nghiệm trên 20 năm trong lĩnh vực sản xuất các loại mousse chống cháy theo tiêu chuẩn của Anh – Mỹ, và các loại Memory Foam, nệm Mousse, nệm lò xo cao cấp, cung cấp cho thị trường trong nước và Nhật Bản. Tuy đã có thời gian hoạt động lâu năm, Công ty vẫn không tránh khỏi những bất cập trong quản lý và sử dụng nguồn nhân lực, gây ảnh hưởng trực tiếp đến năng suất và chất lượng sản phẩm, tạo ra những tổn thất không đáng có.
Nhận thức được những vấn đề còn tồn tại, Ban lãnh đạo của Công ty TNHH Nệm Ưu Việt đã tham gia Chương trình Quốc gia “Nâng cao năng suất và chất lượng sản phẩm, hàng hoá của doanh nghiệp Việt Nam đến năm 2020” của Chính phủ. Với sự hỗ trợ của các chuyên gia tư vấn về năng suất chất lượng của QUATEST 3, Công ty đã tìm ra một số vấn đề tồn tại gây cản trở trong quá trình sản xuất.
Đó là, công việc chưa được phân bổ hợp lý, đội ngũ công nhân tay nghề chưa cao. Nhân sự các bộ phận chưa được đào tạo các kỹ năng liên quan để kiểm soát nhà máy nên các hoạt động cải tiến nhằm nâng cao hiệu quả làm việc của con người và máy móc, thiết bị chưa đạt được yêu cầu như mong muốn, ảnh hưởng đến chất lượng sản phẩm. Bên cạnh đó, nhân viên chưa nhận thức được đầy đủ các tổn thất, lãng phí trong Công ty. Thứ phẩm phát sinh nhiều ảnh hưởng đến chi phí hoạt động của Công ty. Tỷ lệ thành phẩm sử dụng cũng chưa đạt như mong muốn.
Ngoài ra, khu vực xưởng may, mouse có nhiều vật dụng chưa được sàng lọc, sắp xếp gọn gàng. Các kệ chứa vật tư, phụ tùng mới chưa được hiển thị tên vật tư, số lượng rõ ràng. Khu vực cắt vải có nhiều nguyên liệu chờ cắt; nguyên liệu dư thừa, hay nguyên liệu dang dở chưa được sàng lọc, sắp xếp gọn gàng. Khu vực may cũng chưa được sắp xếp phân chia rõ ràng với các khu vực chờ may, hoàn thành, máy may.
Quá trình cải tiến và kết quả đạt được
Sau khi nghiên cứu và phân tích về quy trình sản xuất sản phẩm, các chuyên gia của QUATEST 3 đã xác định nguyên nhân khiến mousse đệm không bằng phẳng là do không có nắp đậy của khuôn đúc, từ đó, phần giữa nhô ra, tạo bề mặt không đồng đều dẫn đến phải cắt xén mousse. Bởi vậy, nhóm chuyên gia đã đưa ra giải đáp là tạo nắp đậy để bề mặt bằng phẳng. Nhờ vào sự cải tiến này, chiều cao các khối thành phẩm tăng từ 650cm lên 700cm, thứ phẩm giảm từ 120cm xuống còn 40cm. Tỉ lệ thành phẩm sử dụng là 94,59% (tăng 12,24%), tương đương 277.32 khối (tăng 35.89 khối mỗi tháng), giúp Công ty tiết kiệm 957 triệu đồng/năm.
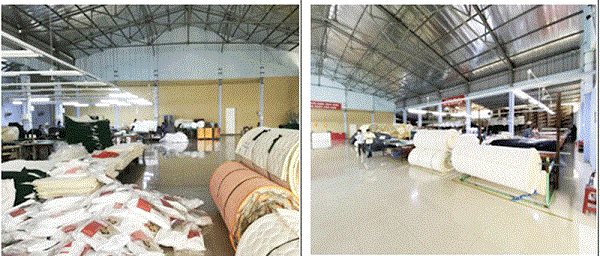
Sau khi cải tiến, Khu vực làm việc được bố trí gọn gàng, phân chia từng khu vực (hình phải) Ảnh: QUATEST 3
Về không gian làm việc, Công ty đã chủ động phối hợp với các chuyên gia của QUATEST 3 để triển khai áp dụng công cụ 5S tại các khu vực có vấn đề. Sau khi triển khai thực hiện 5S tại khu vực cắt may, các khu vực làm việc được phân chia rõ ràng. Vật tư, bán thành phẩm, dụng cụ máy may được sàng lọc, phân loại và sắp xếp gọn gàng, theo khu vực riêng.
Với những kết quả đã đạt được, Ban lãnh đạo Công ty quyết định sẽ tiếp tục mở rộng việc áp dụng các công cụ năng suất sang khu vực khác. Đặc biệt, hướng tới giảm hơn nữa thời gian thực hiện sản phẩm và thời gian giao hàng.
Kiều Anh