Nghiên cứu Áp dụng công nghệ LASER CLADDING nhằm tối ưu hóa quá trình sửa chữa chi tiết máy
Trong bài báo này, trình bày về quy trình công nghệ sửa chữa chi tiết trục xi-lanh dầu dựa trên công nghệ laser cladding. Các thông số lớp phủ, bao gồm công suất laser và quỹ đạo phun, đã được tối ưu hóa để cải thiện chất lượng bề mặt và giảm thiểu khiếm khuyết. Kết quả thí nghiệm cho thấy lợi ích từ việc áp dụng lớp phủ laser LYF01, đặc biệt là với mẫu có tỷ lệ chồng chéo 50% và công suất 2500W. Quy trình này không chỉ cải thiện độ cứng và khả năng chống mài mòn của vật liệu nền mà còn đảm bảo hiệu suất tối ưu trong việc sửa chữa và bảo dưỡng.
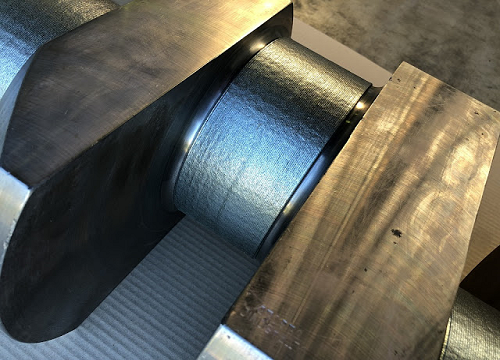
Hiện nay, tại Việt Nam, việc áp dụng máy móc và thiết bị công nghiệp vào sản xuất đang trở nên phổ biến, đặc biệt trong những ngành như thủy điện và khai thác khoáng sản. Các thiết bị này thường có kích thước lớn và được thiết kế phức tạp để đáp ứng yêu cầu của môi trường làm việc khắc nghiệt. Ví dụ, kim phun thủy điện là thiết bị sử dụng áp lực nước cao để thực hiện nhiều nhiệm vụ trong công trình thủy điện, dùng để làm sạch bề mặt bê tông, loại bỏ rong rêu và các chất cặn bã khác từ các bộ phận của đập. Hàng năm, sau những mùa mưa bão, các nhà máy thủy điện làm việc quá công suất dẫn đến các chi tiết như vành chặn, kim phun, cánh dẫn hướng bị ăn mòn, xói mòn và xâm thực nặng. Trong ngành khai thác mỏ, xi-lanh thủy lực của máy phá đá thường tiếp xúc trực tiếp với các điều kiện môi trường có độ ẩm cao, bụi và các chất hóa học có thể gây ăn mòn dẫn đến chi tiết bị hư hỏng nặng và thường phải yêu cầu thay thế. Tuy nhiên, giải pháp thay thế không phải lúc nào cũng là lựa chọn tốt, đặc biệt trong bối cảnh hiện nay tại Việt Nam. Các giải pháp công nghệ mới được xem là một hướng tiếp cận tiết kiệm và bền vững hơn, không chỉ giảm thiểu tác động đến môi trường mà còn kéo dài tuổi thọ các chi tiết máy thay vì thay thế mới. Công nghệ sửa chữa dựa trên công nghệ laser cho phép phục hồi các chi tiết máy bị hư hỏng sử dụng phương pháp hàn bằng kim loại dạng bột. Mục tiêu chính là phục hồi hình dạng và kích thước ban đầu của các chi tiết máy. Công nghệ này được áp dụng rộng rãi trong các ngành như hàng không vũ trụ, chế tạo máy và nhiều lĩnh vực khác. Đặc điểm nổi trội của việc sử dụng công nghệ laser trong sửa chữa là tốc độ sửa chữa nhanh mà vẫn đảm bảo yêu cầu kỹ thuật và chất lượng chi tiết máy.
Công nghệ laser cladding được thực hiện bằng việc sử dụng dây hoặc nguyên liệu dạng bột. Trong quá trình này, tia laser tạo ra một vùng nóng chảy trên bề mặt của vật liệu, trong lúc dây hoặc bột được cung cấp vào đồng thời. Dù nguồn nhiệt từ tia laser có công suất cao, nhưng thời gian tiếp xúc ngắn, làm cho việc đông đặc và làm mát diễn ra nhanh chóng.
Trên thế giới, công nghệ Laser cladding đang là một lựa chọn hàng đầu trong việc sửa chữa và tăng cường bề mặt của các chi tiết máy. Đặc biệt trong các ngành công nghiệp trọng điểm như hàng không vũ trụ, công nghệ ô tô, hóa dầu, luyện kim và đường sắt. Khả năng của công nghệ này được chứng minh qua việc giảm chi phí, tối ưu hóa quy trình và nâng cao chất lượng sản phẩm. Bằng cách sử dụng công nghệ laser cladding, các doanh nghiệp ngoài việc có thể cải thiện và tăng cường các thuộc tính của các bộ phận quan trọng, còn có thể kéo dài tuổi thọ của chúng, giảm tần suất và chi phí bảo dưỡng, sửa chữa. Đã có nhiều công trình nghiên cứu khoa học được công bố và đánh giá, kiểm chứng về tính hiệu quả của công nghệ laser cladding.
Trong bài báo này, nhóm tác giả đã đề xuất và xây dựng quy trình công nghệ sửa chữa chi tiết trục xi-lanh dầu. Ở đây, mô hình 3D của chi tiết hỏng được thiết kế lại. Công nghệ laser cladding được sử dụng làm phương pháp sửa chữa và gia công thứ cấp, được tiến hành trên chi tiết để đảm bảo độ chính xác về kích thước hình học. Ngoài ra, để tăng tính năng cơ học, nhóm nghiên cứu sử dụng LYF01 làm vật liệu bột. Các thông số lớp phủ tối ưu bao gồm công suất laser, khoảng cách giữa đầu laser và phôi, khoảng cách giữa ống cấp bột và phôi, tốc độ phun và khả năng phun, tỷ lệ chồng chéo được nghiên cứu một cách có hệ thống để giảm thiểu các khiếm khuyết bên trong và cải thiện chất lượng bề mặt. Cuối cùng, các đặc tính cơ học của răng tái tạo được kiểm tra và so sánh với chi tiết ban đầu.
Sau khi tiến hành quá trình phun lớp phủ laser, việc kiểm tra nứt vỡ trên bề mặt của lớp phủ là một bước quan trọng để đảm bảo chất lượng và tính đồng nhất của lớp phủ. Phương pháp thẩm thấu, một kỹ thuật không phá hủy, đã được áp dụng trong việc kiểm tra này. Trong quá trình kiểm tra bằng phương pháp thẩm thấu, chất lỏng (thường là chất nhuộm màu) được sử dụng để thẩm thấu vào các khe nứt hoặc lỗ hổng trên bề mặt lớp phủ. Sau một khoảng thời gian cụ thể để thẩm thấu, bề mặt được làm sạch và chất chỉ thị được phun lên. Mọi khe nứt hoặc lỗ hổng sẽ thể hiện rõ ràng dưới dạng các đường màu sắc, do chất nhuộm đã thẩm thấu xuất hiện trên bề mặt dưới tác động của chất chỉ thị.
Kết quả từ phương pháp thẩm thấu đã cho thấy rằng, lớp phủ tạo ra từ công suất 2000W, 2500W, 3000W, 1500W không chỉ có độ nhẵn và độ mịn cao, mà còn không có dấu hiệu của nứt vỡ hoặc lỗ hổng. Điều này thể hiện lớp phủ có độ bám dính tốt và độ đồng nhất cao. Lớp phủ tại mức công suất 1500W và 2000W có bề mặt đẹp, nhưng vẫn tồn tại vấn đề với bột không hoàn toàn nóng chảy, làm giảm hiệu quả chi phí. Đối với lớp phủ ở mức công suất 2700W và 3000W lại gặp vấn đề với hiện tượng cháy trên bề mặt xung quanh vùng nóng chảy và gây ra biến dạng cho phôi, như cong vênh. Do đó, công suất 2500W có bề mặt phủ nhẵn nhất và tối ưu hóa lượng bột tiêu thụ, giúp tiết kiệm chi phí.
Dựa vào kết quả kiểm tra vi cấu trúc SEM ở các công suất khác nhau, rõ ràng mức công suất 2500W cho ra lớp phủ laser với mối liên kết tốt và chất lượng bề nhẵn, không có hiện tượng nứt vỡ và đáp ứng tiêu chuẩn về độ cứng của bột. Tại các độ phóng 1mm và 100µm đề cập đến kích thước của vùng mẫu được quan sát. Đối với 1mm thể hiện hình ảnh tổng quan về toàn bộ khu vực và 100µm cung cấp hình ảnh chi tiết về cấu trúc vi mô của bề mặt. Hai cấp độ phóng đại này giúp nhóm nghiên cứu phân tích các đặc điểm khác biệt trong cấu trúc và mô hình của mẫu vật ở các mức độ khác nhau, từ đó thu thập thông tin chi tiết có giá trị. Kết quả thí nghiệm cho thấy độ dày của lớp phủ tăng theo mức độ gia tăng của công suất laser. Với mẫu có công suất 2500W, độ dày tối đa của lớp chuyển tiếp đạt khoảng 50µm và vùng ảnh hưởng nhiệt của mối hàn khá nhỏ.
Đặc biệt, mẫu có tỷ lệ chồng chéo 50% đã thể hiện độ phẳng tốt nhất. Dựa trên các thí nghiệm, chúng ta xác định rằng các thông số tối ưu cho việc laser cladding với thép CT3 và bột LYF01 là công suất 2500W, tốc độ quét 100mm/phút và tỷ lệ chồng chéo là 50%. Với việc áp dụng lớp phủ laser LYF01, vật liệu nền có độ cứng và khả năng chống mài mòn tăng cao, đảm bảo hiệu suất tối ưu cho quá trình sửa chữa và bảo dưỡng.
Qua nghiên cứu này, nhóm tác giả đã phát triển thành công một quy trình sửa chữa trục xi-lanh dầu sử dụng công nghệ laser cladding, tái thiết kế bằng mô hình 3D và sử dụng vật liệu bột LYF01. Thông qua thí nghiệm, nhóm tác giả xác định được các thông số tối ưu là công suất 2500W, tốc độ quét 100mm/phút và tỷ lệ chồng chéo 50%, cải thiện độ cứng và độ bền chống mài mòn. Quy trình này đã được kiểm chứng không chỉ qua kết quả thí nghiệm mà còn trong áp dụng thực tế, chứng minh tính hiệu quả và tiềm năng ứng dụng rộng rãi
Tạp chí Cơ khí Việt Nam, Số 314, tháng 4 năm 2024