Nâng cao năng suất nhờ sử dụng hiệu quả trang thiết bị, máy móc
Để thực hiện phương pháp quản lý TPM hiệu quả, doanh nghiệp cần hiểu một cách tổng quát các tổn thất liên quan đến thiết bị nhằm loại bỏ lãng phí, tổn thất để nâng cao năng suất, chất lượng sản phẩm.
TPM (Total Productive Maintenance) là phương pháp quản lý hướng tới đổi mới trong hoạt động bảo dưỡng với sự tham gia của mọi cán bộ, nhân viên trong doanh nghiệp. Phương pháp này đảm bảo hiệu quả thiết bị, nâng cao năng suất, chất lượng sản phẩm và môi trường làm việc an toàn. Tuy nhiên, có một thực tế là đa phần doanh nghiệp thường quan tâm đến đầu tư, đổi mới trang thiết bị máy móc nhưng thường quên hoặc ít quan tâm đến việc sử dụng hiệu quả trang thiết bị máy móc. Vì vậy, để thực hiện TPM hiệu quả, doanh nghiệp cần hiểu được một cách tổng quát các tổn thất liên quan đến thiết bị nhằm loại bỏ lãng phí, tổn thất để nâng cao năng suất, chất lượng sản phẩm.
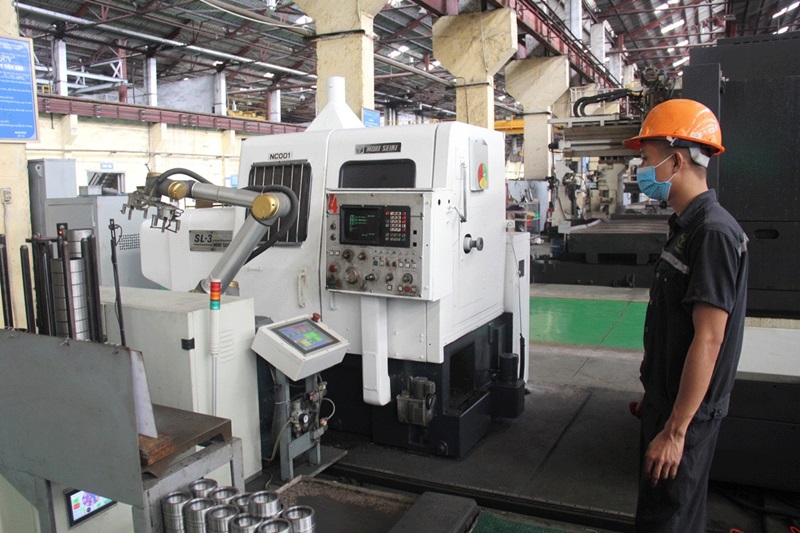
Hiểu được các tổn thất liên quan đến thiết bị giúp doanh nghiệp nâng cao năng suất, chất lượng sản phẩm. Ảnh minh họa.
Thiết bị bị lỗi hoặc hỏng hóc
Yếu tố đầu tiên trong “6 tổn thất lớn” cần phải loại trừ là thiết bị bị lỗi, hỏng hóc và thời gian chết của thiết bị. Có 2 loại hỏng hóc cơ bản, đó là dạng hỏng hóc xảy ra ngẫu nhiên và dạng hỏng hóc xảy ra thường xuyên.
Tần suất xảy ra hỏng hóc thường xuyên càng gia tăng sẽ dẫn tới hậu quả là tần suất các hỏng hóc ngẫu nhiên cũng gia tăng theo, điều đó đồng nghĩa với việc thiết bị càng dễ và nhanh hư hại. Nói cách khác, bất kỳ tổn thất nào được loại trừ giúp làm tăng thời gian hoạt động cũng như hệ số sẵn sàng của thiết bị.
Cài đặt và hiệu chỉnh thiết bị
Loại tổn thất thứ hai là các công việc chuẩn bị trước khi sản xuất. Để chuẩn bị cho sản xuất, những người thợ cơ khí, bảo dưỡng thường tốn rất nhiều thời gian cho công việc chuẩn bị máy. Có một hệ thống giúp công việc chuẩn bị đạt hiệu quả đó là tính thời gian chết - SMED (Single Minute Exchange of Die). Hệ thống này có nguồn gốc từ Nhật Bản, do Shigeo Shingo sáng tạo và phát triển. Có hai yếu tố tiêu điểm mà SMED tập trung nhằm loại bỏ hoặc giảm thiểu là:
Thời gian chuẩn bị cho các yếu tố bên trong thiết bị (thời gian khi thiết bị ngừng hoạt động) và thời gian chuẩn bị các yếu tố bên ngoài (thời gian khi thiết bị đang hoạt động); Yếu tố còn lại là sự điều chỉnh thông số kỹ thuật của máy móc thiết bị... để hoàn thành công việc chuẩn bị trước khi sản xuất; Nếu áp dụng kỹ thuật SMED có thể giúp giảm thời gian chuẩn bị, khoảng thời gian này chuyển sang thành thời gian hoạt động của thiết bị. Như vậy, việc áp dụng kỹ thuật SMED sẽ làm gia tăng đáng kể hệ số sẵn sàng của thiết bị.
Thiết bị bị gián đoạn khi đang vận hành
Thiết bị bị gián đoạn khi đang vận hành là nguyên nhân lớn nhất gây ra thời gian chết của máy. Vì vậy, duy trì trạng thái làm việc tốt nhất của thiết bị, thiết lập chương trình đào tạo hiệu quả, thực hiện các phương thức vận hành hiệu quả và đúng tiêu chuẩn là cách duy nhất để loại trừ được những nguyên nhân gây nên gián đoạn không cần thiết.
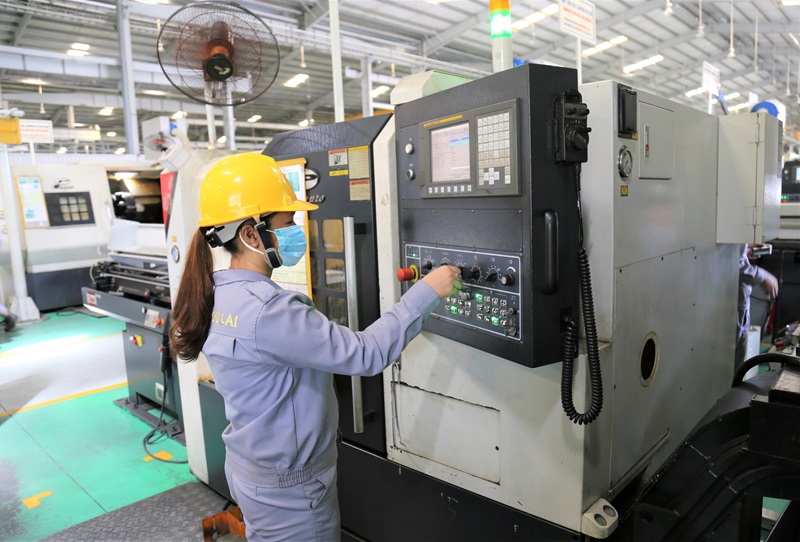
Bất kỳ tổn thất nào được loại trừ sẽ giúp làm tăng thời gian hoạt động cũng như hệ số sẵn sàng của thiết bị. (Ảnh minh họa)
Tốc độ vận hành bị giảm sút
Nguyên nhân gây ra sự giảm sút tốc độ vận hành của thiết bị là do máy móc không được vận hành theo đúng tốc độ được thiết kế ban đầu. Hệ số suy giảm tốc độ là sự khác nhau giữa tốc độ của thiết bị được thiết kế của nhà sản xuất và tốc độ vận hành thật sự của thiết bị trong điều kiện sản xuất bình thường. Để gia tăng tốc độ của máy cần phải tìm ra nguyên nhân từ đó ta có thể dễ dàng tìm cách giải quyết hiệu quả vấn đề trên.
Sản phẩm đầu ra bị khuyết tật
Sản phẩm bị khuyết tật có thể xem là căn bệnh tổn thất mãn tính của bất kỳ hệ thống sản xuất nào. Những tổn thất do vấn đề này gây nên bao gồm: Nhân viên phải tốn nhiều thời gian hơn cho việc kiểm tra đầu ra; Hệ thống sản xuất bị tắc nghẽn tại khu vực kiểm tra đầu ra; Thời gian để xử lý các sản phẩm không phù hợp tiêu chuẩn; Hệ thống sản xuất bị gián đoạn do sản phẩm dở dang bị lỗi. Chi phí của một sản phẩm sản xuất bất kỳ bao gồm chi phí nguyên vật liệu và chi phí lao động. Do vậy, để tiết kiệm chi phí, hạn chế tổn hao về tài chính mỗi doanh nghiệp sản xuất nói chung cần phải xem nó như là một loại tổn thất cá biệt để tìm cách loại bỏ hoàn toàn.
Hiệu suất thiết bị giảm sút
Dấu hiệu của hiệu suất thiết bị giảm là các thiết bị thường xuyên vận hành ở tốc độ thấp, sản phẩm lỗi xuất hiện thường xuyên trong quá trình sản xuất và bị đẩy ra khỏi băng chuyền. Trong thời gian này, cần phải có những điều chỉnh cần thiết và kịp thời nhằm ổn định lại hệ thống sản xuất.
Cần hiểu rằng không có bất cứ phép màu nào có thể biến chuyển một thiết bị có năng suất thấp trở nên đạt hiệu quả cao trong quá trình sản xuất. Tuy nhiên, công ty sản xuất có thể cải thiện hiệu suất hoạt động của máy móc nếu giải quyết được các vấn đề như: kiểm soát vận hành không hợp lý, thiếu hoạt động đào tạo và các chương trình giáo dục kiến thức, kỹ năng cần thiết; kỹ thuật điều hành không phù hợp; thiếu quy trình, phương pháp điều hành hiệu quả và đạt tiêu chuẩn cho cấp quản lý cũng như nhân viên vận hành. Tư duy “hỏng đâu sửa đó” là nguyên nhân chính gây nên “6 tổn thất lớn” của thiết bị được đề cập ở trên và cũng được xem là nguyên nhân cốt lõi làm cho thiết bị không đạt hiệu quả trong quá trình sản xuất.